2023 Federal Updates Navigating the Changing Landscape of Health and Safety Regulations
Welcome to Osha Journal’s dedicated page for “2023 Federal Updates.” We understand that staying current with evolving health and safety regulations is essential for ensuring workplace safety and compliance. This page is your comprehensive resource for keeping up-to-date with the latest changes in federal guidelines and standards for occupational health and safety in the year 2023.
The year 2023 brings with it a fresh set of federal updates in the realm of workplace safety and health. These updates can influence everything from regulatory compliance to safety practices and standards within your organization. Our mission is to keep you well-informed about these changes, enabling you to adapt and thrive in a dynamic regulatory landscape.
5 OSHA Rule Changes for 2023
As the calendar rolls over to 2023, sites that resolve to make safety a priority will have some new rules and regulations to incorporate. The Spring Unified Agenda covering all federal agencies revealed OSHA has big plans in the works.
Here are 5 upcoming OSHA rule changes you should know including: OSHA recordkeeping requirements, Lockout-Tagout changes, silica exposure considerations, heat exposure regulations, and updated HazCom classifications and shipping requirements.
1- Recordkeeping Proposed Rule
The U.S. Department of Labor’s Occupational Safety and Health Administration is proposing amendments to its occupational injury and illness recordkeeping regulation, 29 CFR 1904.41. The current regulation requires certain employers to electronically submit injury and illness information – that they are required to keep – to OSHA. The agency uses these reports to identify and respond to emerging hazards and makes aspects of the information publicly available.
In addition to reporting their Annual Summary of Work-Related Injuries and Illnesses, the proposed rule would require certain establishments in certain high-hazards industries to electronically submit additional information from their Log of Work-Related Injuries and Illnesses, as well as their Injury and Illness Incident Report.
As part of OSHA’s mission to protect workers and mitigate workplace hazards, this rule would improve OSHA’s ability to use its enforcement and compliance assistance resources to identify workplaces where workers are at high risk. The proposed rule would also advance the department’s mission to empower workers by increasing transparency in the workforce.
The proposed rule would
- Require establishments with 100 or more employees in certain high-hazard industries to electronically submit information from their OSHA Forms 300, 301 and 300A to OSHA once a year.
- Update the classification system used to determine the list of industries covered by the electronic submission requirement.
- Remove the current requirement for establishments with 250 or more employees not in a designated industry to electronically submit information from their Form 300A to OSHA annually.
- Require establishments to include their company name when making electronic submissions to OSHA.

2- Lockout-Tagout (LOTO) Update
The Control of Hazardous Energy standard (29 Code of Federal Regulations [C.F.R.] 1910.147), commonly known as Lockout Tagout (LOTO) under the Occupational Safety and Health Administration (OSHA) has been relatively untouched since it was published in 1989.
LOTO infractions are one of the persistent and most-cited OSHA standards. The top 10 frequently cited LOTO infractions include a failure to:
- HAVE EQUIPMENT-SPECIFIC LOTO PROCEDURES
- TRAIN WORKERS IN LOTO
- CONDUCT PERIODIC INSPECTIONS
- ESTABLISH A LOTO PROGRAM
- FOLLOW THE SEQUENCE OF LOTO
- PROTECT WORKERS DURING GROUP LOTO OPERATIONS
- IDENTIFY ALL OR DISCONNECT ALL ENERGY SOURCES
- NOTIFY EMPLOYERS
- MANAGE SHIFT CHANGES
- FOLLOW THE “SERVICING AND TOOL CHANGE” EXCEPTION

3- Silica Update
In 2016, OSHA issued two new standards for respiratory crystalline silica (RCS) ? one for general industry and maritime (29 CFR ? 1910.1053) and one for construction (29 CFR ? 1926.115).
The 2016 standards established an exposure action level (AL) of 25 ?g/m3 and reduced the silica PEL from 100 to 50 ?g/m3- both calculated as 8-hour time-weighted averages (TWAs). The standards include requirements for installing exposure controls, implementing medical surveillance programs to monitor workers’ health and exposure to RCS, and maintaining a written exposure control plan.
OSHA standards for other chemicals have medical removal provisions such as lead, cadmium, and formaldehyde. Each require the employer to monitor certain exposure indicators such as airborne concentrations of chemicals or bloodborne concentrations (as in the case of lead exposure) and remove the employee from the source of exposure once specified maximum levels are reached. Following publication of the 2016 final rules, the US Court of Appeals for the District of Columbia Circuit concluded that OSHA failed to adequately explain its decision to omit medical removal protections from the rule and remanded the rule for further consideration of the issue.
The Spring Regulatory Agenda contains an initiative called “Occupational Exposure to Crystalline Silica: Revisions to Medical Surveillance Provisions for Medical Removal Protection.” OSHA is planning to revisit the silica rules to include medical removal provisions with an estimated timeframe of May 2023 for publication of an NPRM.
Employers subject to the silica rules will need to be sure they have thorough workplace inspection and industrial hygiene (IH) medical surveillance programs in place, and an efficient incident management system to enable prompt recording of medical removal cases.
4- Regulatory Activities on Heat Exposure
According to the U.S. Department of Labor’s Bureau of Labor Statistics (BLS), hazardous heat exposure resulted in an average of 35 fatalities per year and 2,700 cases with multiple days away from work between 2015 and 2019. The BLS indicates that heat-related fatalities may be underreported and improperly diagnosed due to failures to document when exposures to heat caused or contributed to “official” causes of death, such as heart attacks.
OSHA published an Advanced Notice of Proposed Rulemaking (ANPRM) in the Federal Register on October 27, 2021, to initiate the process of work on a heat exposure standard. The purpose of the ANPRM is to “more clearly set forth employer obligations and the measures necessary to more effectively protect employees from hazardous heat.”
OSHA rolled out a new National Emphasis Program (NEP) on “Outdoor and Indoor Heat-Related Hazards” on April 8, 2022. The NEP lays out OSHA’s inspection and enforcement priorities to support reduction of occupational illnesses and fatalities from heat exposure.

5- HazCom Proposed Rule
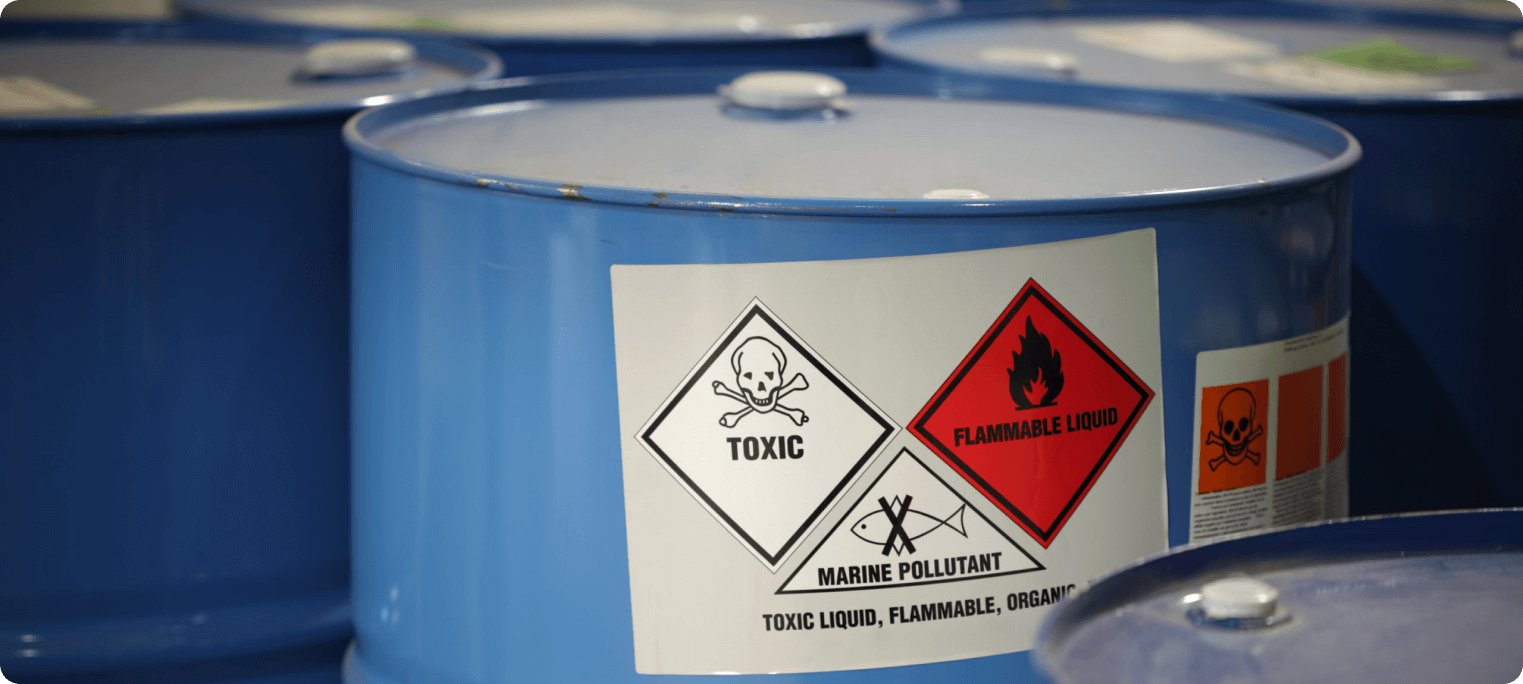
OSHA's New Plan for Workplace Safety in 2023
The Occupational Safety and Health Administration (OSHA) is the federal agency responsible for ensuring safe and healthy working conditions for employees across the United States. In January 2023, OSHA announced an aggressive new plan to address workplace safety, including several key initiatives aimed at reducing injuries and fatalities in the workplace. The Biden administration is focused on increasing its investigation and enforcement activity against employers in the coming months/years.
In this post, we will take a closer look at OSHA’s new initiatives and provide some tips for employers on how they can improve workplace safety.
OSHA’s new plan for workplace safety in 2023 has several key areas that will attempt to improve working conditions for employees across the country. These initiatives include: