Common Violations
Welcome to the OSHA Journal’s comprehensive guide on common workplace safety violations. In the pursuit of a safe and healthy work environment, it is imperative that employers, employees, and safety professionals alike are well-informed about the potential hazards that can arise in various industries.
Workplace safety violations encompass a wide range of issues, from electrical hazards to hazardous materials handling, falls, and more. Understanding these common violations is the first step toward preventing accidents, injuries, and costly legal consequences. This page is dedicated to providing you with essential knowledge on the subject, helping you navigate the complex landscape of safety regulations.
As you delve into the following sections, you will gain insights into the types of violations that frequently occur across industries, the potential risks associated with each violation, and the critical importance of compliance with Occupational Safety and Health Administration (OSHA) regulations. We will also explore practical steps for prevention, share real-world examples, and offer resources to enhance your workplace safety efforts.
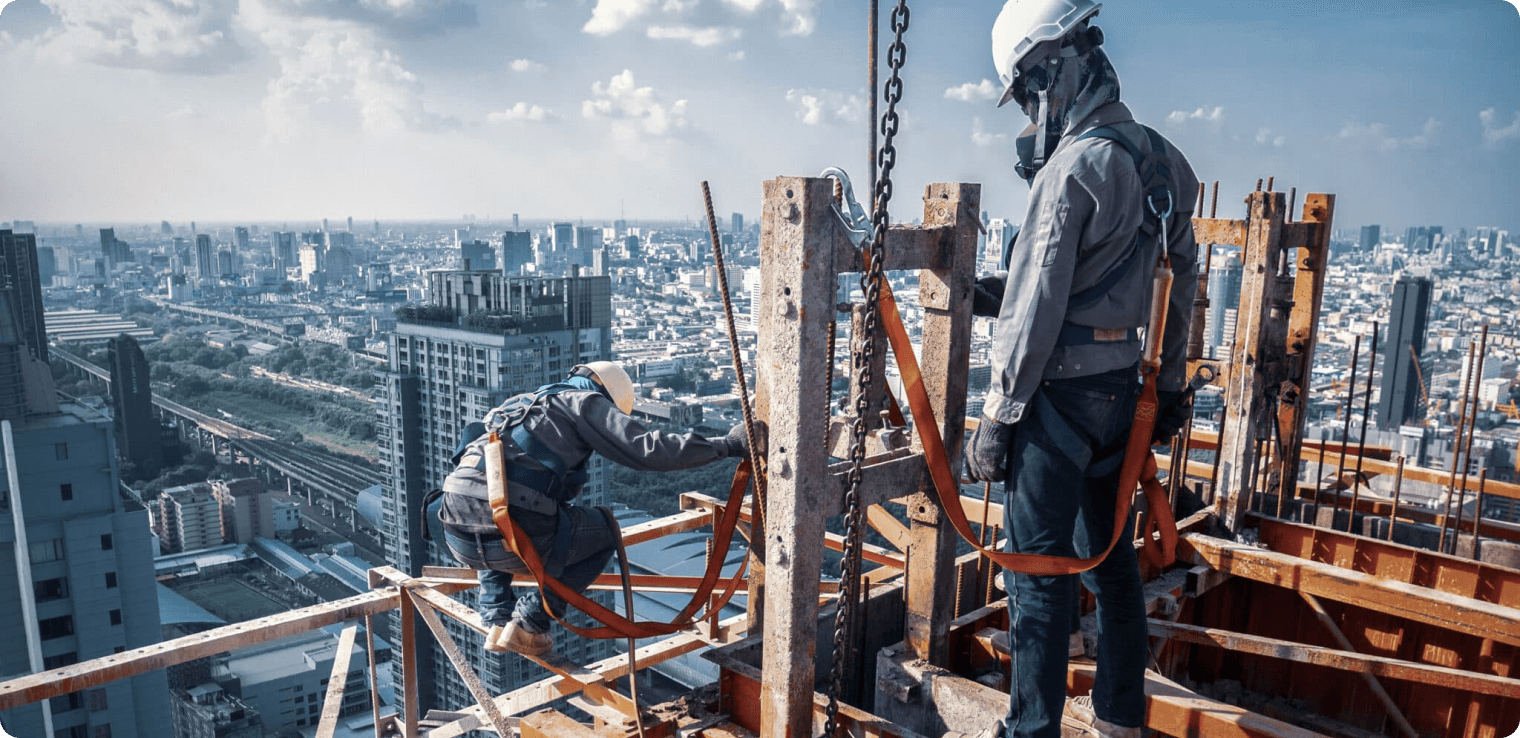
Whether you are an employer looking to safeguard your employees and company’s reputation or an employee seeking to better understand your rights and responsibilities, this page serves as a valuable resource. Workplace safety is a shared responsibility, and together, we can work towards creating safer and healthier workplaces for everyone.
Navigate through the sections below to gain a comprehensive understanding of common violations and how to address them effectively. Your commitment to safety is a vital component of a thriving, injury-free workplace.
Top 10 Most Common Violations
Every year, thousands of workplace safety violations are reported across various industries. These violations pose significant risks to employees and can result in injuries, illnesses, and even fatalities. To raise awareness and promote a safer work environment, we’ve compiled a list of the top 10 most common workplace safety violations
1- Fall Protection
Employers must protect employees from fall hazards and falling objects, and ensure elevated working surfaces have structural integrity.
2- Hazard Communication
3- Scaffolding
Unsafe scaffolding practices, including inadequate assembly, inspection, and use, leading to falls and injuries.
4- Respiratory Protection
5- Lockout/Tagout
6- Powered Industrial Trucks
7- Ladders
8- Machine Guarding
9- Electrical Wiring Methods
10- Fall Protection - Training Requirements
Insufficient training for employees exposed to fall hazards, including failing to educate workers on recognizing and avoiding fall risks.
Understanding the Impact
Workplace safety violations are not mere paperwork or regulations; they have tangible, often life-changing consequences. Understanding the impact of safety violations is crucial in emphasizing the importance of adhering to safety protocols. In this section, we will delve into the real-world consequences that workers and employers can face when safety is compromised.
Consequences of Safety Violations
Injuries
Fatalities
Tragically, some safety violations can lead to fatal accidents. The loss of a colleague, friend, or family member due to a preventable workplace incident is a devastating consequence that affects not only the immediate workplace but also the entire community.
Health Issues
Prolonged exposure to unsafe working conditions can result in chronic health problems. For example, exposure to hazardous chemicals or lack of proper ventilation can lead to respiratory diseases, while repetitive motion without ergonomic safeguards can cause musculoskeletal disorders.
Legal Penalties
Employers who fail to uphold safety standards may face legal consequences. This can include fines, penalties, and even criminal charges, depending on the severity of the violations. These legal ramifications can have a lasting impact on a company’s reputation and financial stability.
Reputation Damage
Beyond legal penalties, safety violations can tarnish a company’s reputation. News of workplace accidents or unsafe practices can deter potential employees, customers, and business partners, leading to long-term financial losses.
Financial Costs
Workplace accidents and injuries result in direct and indirect financial costs. Employers may need to cover medical expenses, workers’ compensation claims, and temporary staffing to fill in for injured workers. These costs can strain a company’s budget.
Emotional Toll
Workplace accidents can take an emotional toll on both employees and employers. Witnessing or being involved in a safety incident can lead to trauma, anxiety, and decreased morale among workers.
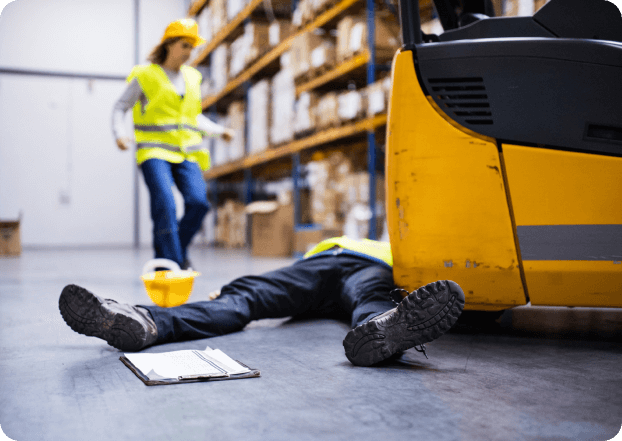
Violation Fines: Minimums and Maximums
Here’s a table of minimum and maximum fines for OSHA violations.
Type of Violation | Minimum Penalty | Maximum Penalty |
---|---|---|
Serious | $1,036 per violation | $14,502 per violation |
Other-than-serious | $0 per violation | $14,502 per violation |
Willful or Repeated | $10,360 per violation | $145,027 per violation |
Posting Requirements | $0 per violation | $14,502 per violation |
Failure to Abate | N/A | $14,502 per day past the abatement date. |
Reporting and Correcting Violations
Reporting and correcting safety violations is a vital step in maintaining a safe and compliant workplace. When these violations occur, it’s essential to take immediate action to protect employees and prevent further incidents. In this section, we’ll guide you through the process of reporting and correcting safety violations effectively.
Reporting Safety Violations
Immediate Action
Internal Reporting
Employers should establish clear internal reporting mechanisms. Encourage employees to report violations to their immediate supervisors or safety officers. Ensure that the reporting process is confidential and non-punitive to encourage reporting.
Anonymous Reporting
OSHA Reporting
Certain violations must be reported directly to OSHA. Ensure that employees are aware of their rights to report safety concerns to OSHA if their employer fails to address them adequately.
Correcting Safety Violations
Immediate Corrective Actions
Root Cause Analysis
Develop Corrective Plans
Create a detailed plan to correct the violation. This plan should include timelines, responsibilities, and resources needed for correction.
Employee Involvemen
Involve employees in the corrective process. They often have valuable insights and suggestions for improving safety measures.
Documentation
Maintain thorough documentation of the violation, the corrective actions taken, and the follow-up steps. This documentation may be necessary for regulatory compliance and future reference.
How are OSHA Violations Discovered?
OSHA violations can continue for many months, or even years before they are discovered. The longer they are allowed to persist, the greater the penalty will be when they are eventually discovered. It is therefore important for OSHA-covered entities to conduct regular OSHA compliance reviews (this is required by the OSHA law) to make sure OSHA violations are discovered and corrected before they are identified by regulators.
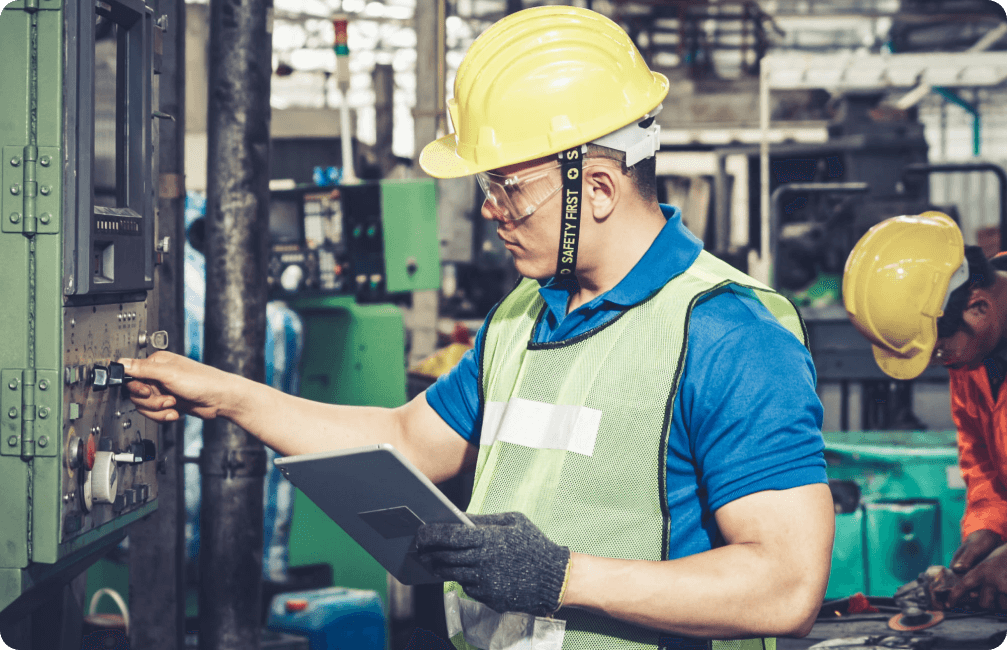
Knowledge Base
- What is OSHA Compliance
- How to Become Compliant
- Understanding Complaints Against You
- Why is a Risk Assessment Important
- Why are Policies & Procedures Important
- What is Joint Responsibility
- Common Violations
OSHA conducts regular, planned inspections of workplaces to ensure compliance with safety and health regulations. These inspections are often scheduled in advance and are based on various factors, including industry hazards, injury rates, and past compliance history.
OSHA may also conduct unannounced or surprise inspections in response to complaints, referrals, or reports of imminent danger.